Where are Encoders Used in the Oil Industry?
Where do encoders face their toughest operating conditions? One answer at the top of the list is in the petroleum industry, where encoders are used everywhere.
In this post we’ll look at encoders in the oil industry, from beginning to end–the rough conditions encoders face on oil drilling rigs, how they keep oil flowing in transport pipelines, and the way they ensure accuracy at gasoline pumps.
ENCODERS PERFORM ON OIL RIGS
Massive drilling systems called oil rigs begin the process of extracting oil from underground reservoirs. Sections of drill pipe are linked together with weights and a bit at the end to form the drill string. The bit bores a hole through earth and rock, sometimes to a depth of thousands of feet.
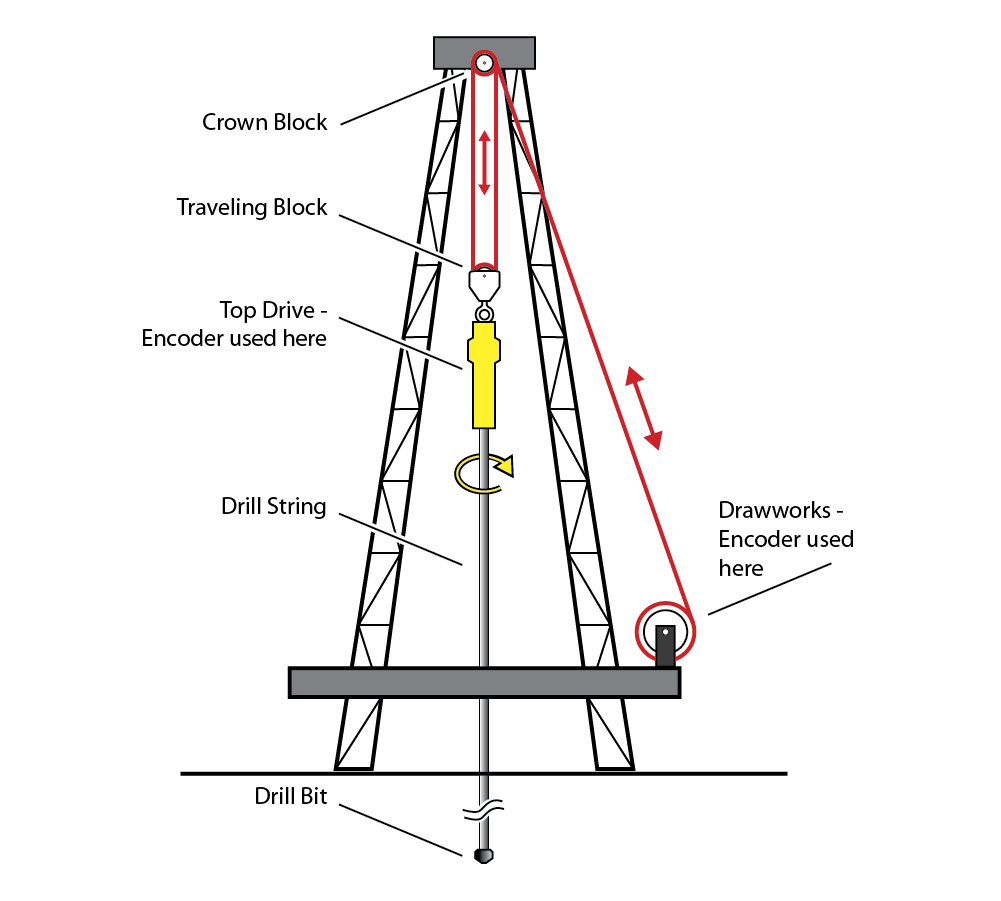
Encoders can be used to help control two critical motions in drilling: rotational speed control while turning the drill string using a top drive or turntable; and vertical position control when using a powerful winch called a drawworks to raise or lower the drill string and top drive. In either case, the working conditions can be horrendous, with vibration, impact, temperature extremes and even explosive fumes being some of the challenges faced.
Top Drive - To cut into rock, the drill string and bit are driven at precise speeds by a top drive, which in modern rigs has replaced older turntable drives. The top drive consists of a motor and gears that rotate the drill string. Precise speed control is critical. Too slow, and drilling time and equipment usage is wasted. Too fast, and the bit or drill pipe can break.
An encoder can be used on the motor or gearbox to monitor rotation speed. The encoder provides feedback so that speed can be precisely controlled to keep torque at optimum levels.
Drawworks - The top drive, drill pipe and bit move up and down via a traveling block and tackle, which is raised and lowered by the drawworks. The combined weight of the load can be hundreds of thousands of pounds.
Position control is crucial. How much pipe has gone down the hole? How deep is the well? Encoders can be used on the drawworks to monitor motor or gear rotation. This helps keep track of the traveling block’s position, and thus the depth of the drilling equipment. Knowing the precise position helps rig operators track whether or not they are on schedule, know what type of rock they’re drilling through, and identify when to change drill bits, for example.
You can see a top drive and drawworks go through their moves in this short video.
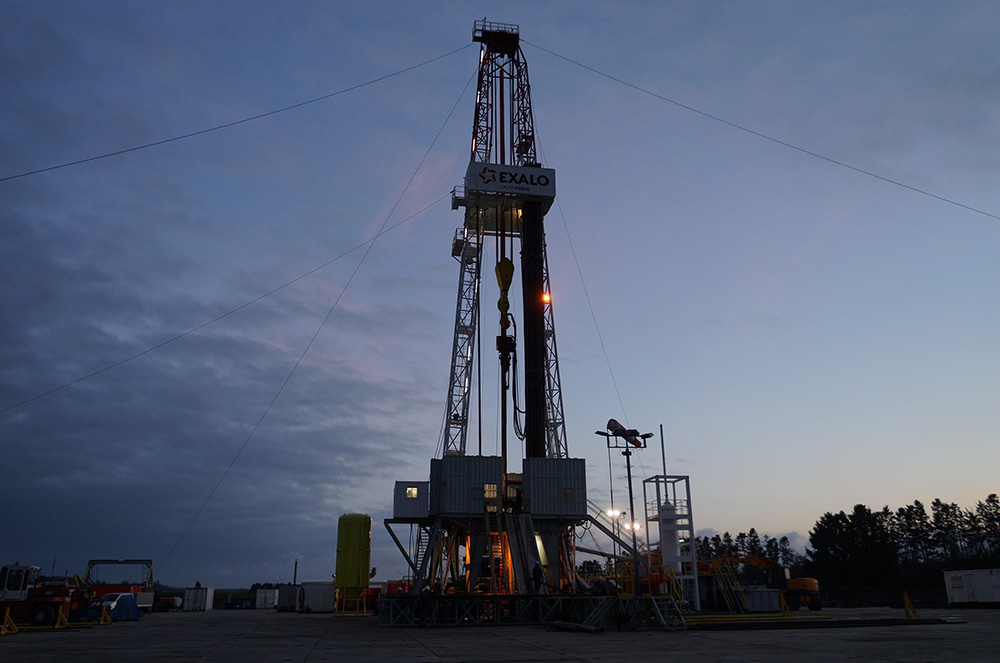
Surviving Harsh—and Dangerous—Conditions - Encoders on oil rigs have extra demands placed on them, even when compared to the most challenging industrial settings. They must operate in harsh conditions while withstanding constant vibration, impact, excessive moisture, dirt, electrical noise, corrosive salt atmosphere, and temperature extremes from deserts to the arctic. And if that’s not enough, they face potentially explosive fumes—even under normal conditions—and must function without causing explosions.
To meet these demands, reliability is key. Manufacturers have developed encoders that can communicate over long distances without signal degradation. Sometimes multiple encoders are stacked up on the same motion axis for redundancy, and also to send signals to different parts of the operation. Some encoders are designed to be certified explosion proof or flameproof, to meet regulatory requirements around the world.
ENCODERS HELP CONTROL FLOW IN TRANSPORT PIPELINES
Once the crude oil has been pumped from the ground, the next challenge is to transport it to a tanker ship or refinery. Pipelines accomplish this task.
Encoders can help here, too. Oil is forced through pipelines at pumping stations, where pumps are driven by motors. Encoders attached to the motors can send feedback to the control system, which uses the encoder signals to maintain precise speed control of the motor and pump.
Encoders help provide constant flow velocity, which is critical. To see why, consider the momentum of oil when it flows through a pipeline.
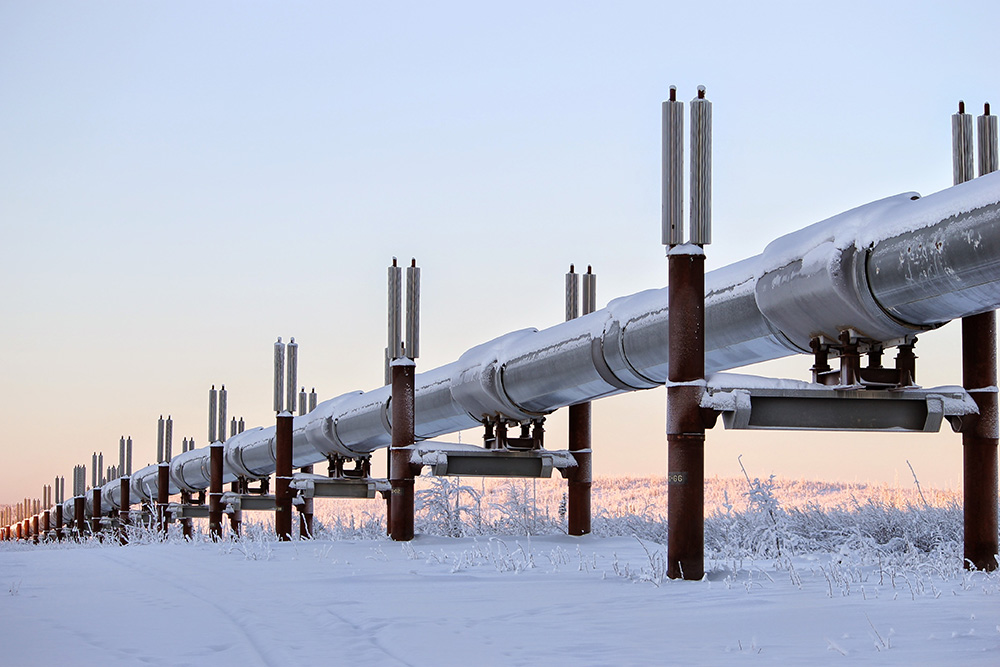
The Trans Alaska Pipeline System, for instance, built in the 1970s, transports oil more than 800 miles across the state of Alaska. The journey takes about 16 days at a velocity of 2 miles per hour in the pipeline. Here are some throughput flow rates from March, 2016 (as per FACTS: Trans Alaska Pipeline System):
544,445 barrels/day = 15,880 gallons/minute = 265 gallons/second
Crude oil weighs about 7.2 pounds per gallon, which means that even at the leisurely pace of 2 miles per hour, more than 1,900 pounds of oil flow by every second. That’s more than 6 barrels per second! If the velocity of the moving flow changes too rapidly, a pressure surge can result and quickly propagate through the pipeline. With encoder feedback used for speed control, pumps can maintain a constant flow, which helps avoid pressure surges and spikes, noise and vibration.
Other pipelines may differ in travel time or flow rates, but no matter what the numbers, encoders can help petroleum products get to their destination smoothly and safely.
ENCODERS DELIVER ACCURACY IN GASOLINE PUMPS AND FUEL DISPENSERS
A large fraction of crude oil pumped from wells is converted to gasoline at refineries. The gasoline is delivered via distribution pipelines and trucks to gas stations, where it’s stored in underground tanks that can hold thousands of gallons. As the gas flows into a customer’s tank, an encoder helps to accurately measure the quantity delivered.
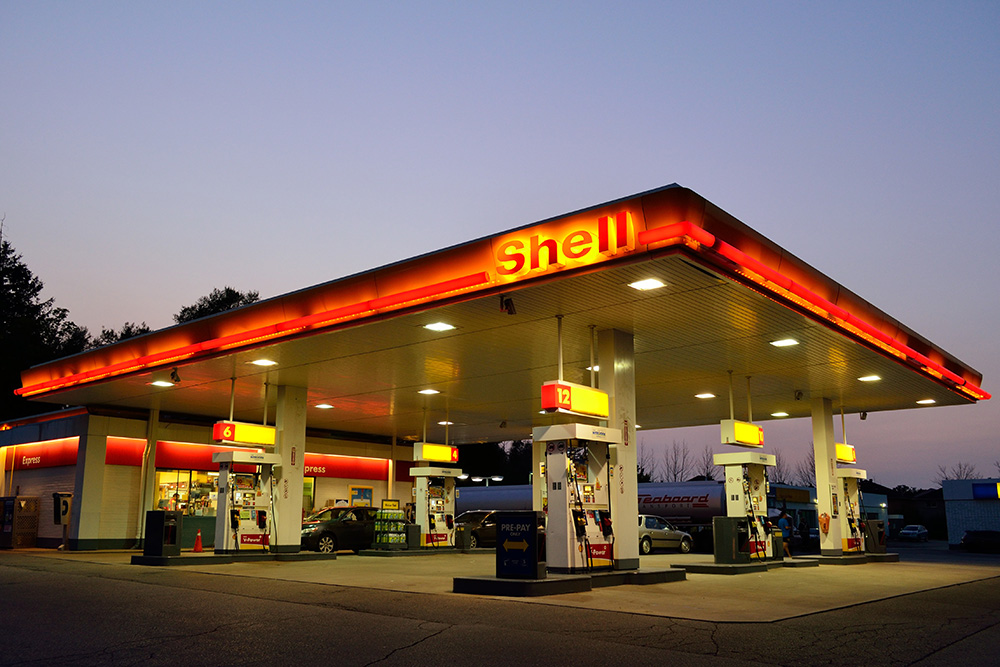
‘Gas Pump’ vs. ‘Fuel Dispenser’ - Before we explain how an encoder performs the trick of measuring a fast-moving flammable liquid, let’s clarify our terms. A gas pump is a self-contained unit that has a pump, a motor to drive the pump, and a flow meter; it draws fuel from the underground tank via a suction line. A fuel dispenser does not have its own pump; instead, a submersible pump is located in the underground tank, which can deliver gas to several dispensers, each with their own flow meter. Most modern gas stations use fuel dispensers, not self-contained gas pumps.
The flow meter is the heart of the dispenser. A variety of technologies are used to measure flow, and in each of them the flowing liquid causes movement in the meter’s mechanism. In prior decades, the meter’s movement was connected directly to a series of linked wheels with numbers on them, which rotated like an odometer to measure gasoline flow.
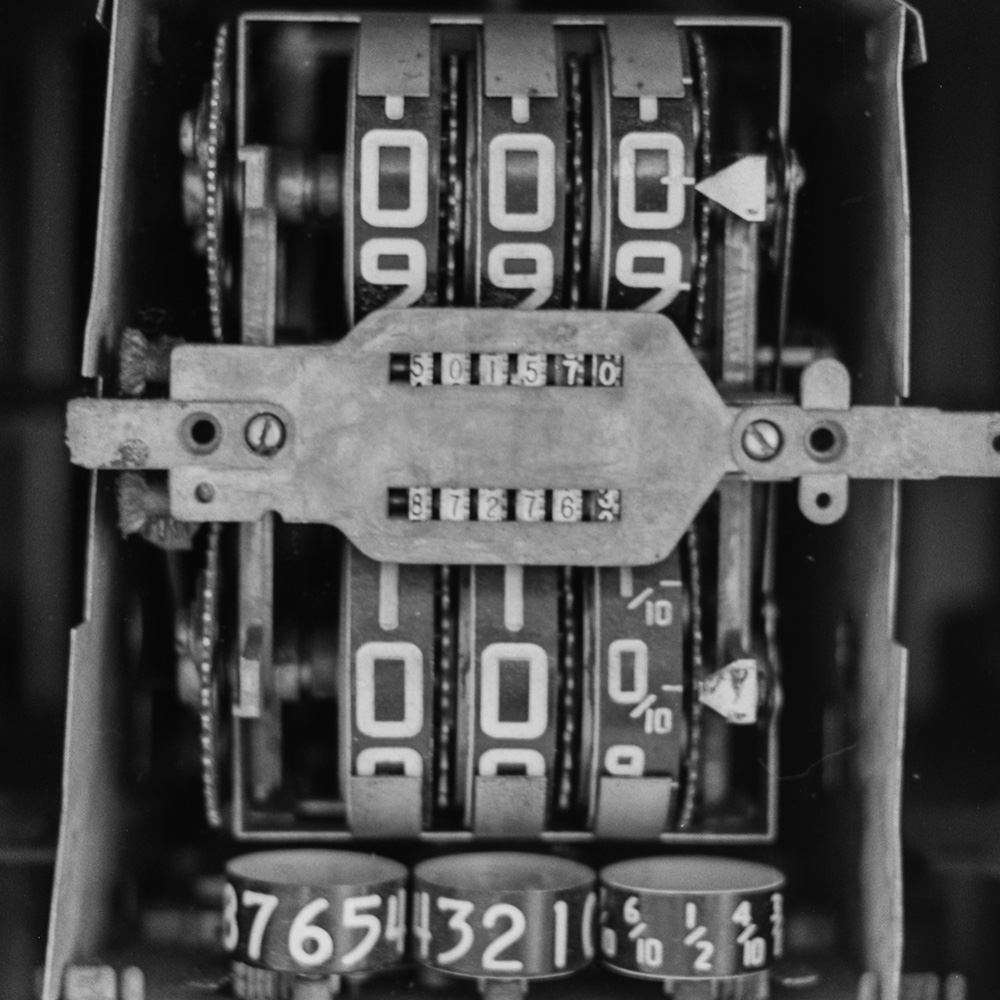
In modern dispensers, the meter’s rotational movement can be connected to a rotary encoder. The encoder transmits signals to a computer, which makes possible all the innovations we’ve come to expect at gas stations: digital displays showing volume and price, pay-at-the-pump by credit card, remote monitoring by staff, and much more. Using an encoder also simplifies the filling process–no need to reset the rotating wheels–which makes it easier for customers to pump their own gas.
Encoders are used everywhere in the petroleum industry: they’re at the beginning when oil is still underground, in the middle when encoders ensure reliable transport, and at the end when they accurately measure gasoline flowing into a customer’s fuel tank.
More in News
Stay up to date
Sign up for our newsletter to stay up to date with our product updates, blog posts, videos and white papers.